בתהליך הפיתוח המשגשג של תעשיית המוליכים למחצה, גביש יחיד מלוטשפרוסות סיליקוןממלאים תפקיד מכריע. הם משמשים כחומר בסיסי לייצור מגוון של מכשירים מיקרואלקטרוניים. החל ממעגלים משולבים מורכבים ומדויקים ועד למיקרו-מעבדים במהירות גבוהה וחיישנים רב-תכליתיים, גביש יחיד מלוטשפרוסות סיליקוןהם חיוניים. ההבדלים בביצועים ובמפרטים שלהם משפיעים ישירות על האיכות והביצועים של המוצרים הסופיים. להלן המפרטים והפרמטרים הנפוצים של פרוסות סיליקון גבישיות יחיד מלוטשות:
קוטר: גודל פרוסות סיליקון גבישיות יחידות מוליכים למחצה נמדד לפי קוטרן, והן מגיעות במגוון מפרטים. קטרים נפוצים כוללים 2 אינץ' (50.8 מ"מ), 3 אינץ' (76.2 מ"מ), 4 אינץ' (100 מ"מ), 5 אינץ' (125 מ"מ), 6 אינץ' (150 מ"מ), 8 אינץ' (200 מ"מ), 12 אינץ' (300 מ"מ) ו-18 אינץ' (450 מ"מ). קטרים שונים מתאימים לצרכים שונים של ייצור ודרישות תהליך. לדוגמה, פרוסות בקוטר קטן יותר משמשות בדרך כלל עבור התקנים מיקרואלקטרוניים מיוחדים בנפח קטן, בעוד שפרוסות בקוטר גדול יותר מפגינות יעילות ייצור גבוהה יותר ויתרונות עלות בייצור מעגלים משולבים בקנה מידה גדול. דרישות פני השטח מסווגות כמלוטש חד צדדי (SSP) וליטוש דו צדדי (DSP). פרוסות מלוטשות חד צדדיות משמשות עבור התקנים הדורשים שטוחות גבוהה בצד אחד, כגון חיישנים מסוימים. פרוסות מלוטשות דו צדדיות משמשות בדרך כלל עבור מעגלים משולבים ומוצרים אחרים הדורשים דיוק גבוה בשני המשטחים. דרישות משטח (גימור): SSP מלוטש חד-צדדי / DSP מלוטש דו-צדדי.
סוג/חומר ממכר: (1) מוליך למחצה מסוג N: כאשר אטומי טומאה מסוימים מוכנסים למוליך למחצה הפנימי, הם משנים את המוליכות שלו. לדוגמה, כאשר מוסיפים יסודות חמש-ערכיים כמו חנקן (N), זרחן (P), ארסן (As) או אנטימון (Sb), אלקטרוני הערכיות שלהם יוצרים קשרים קוולנטיים עם אלקטרוני הערכיות של אטומי הסיליקון הסובבים אותם, ומשאירים אלקטרון נוסף שאינו קשור בקשר קוולנטי. כתוצאה מכך, ריכוז אלקטרונים גדול מריכוז החור יוצר מוליך למחצה מסוג N, המכונה גם מוליך למחצה מסוג אלקטרונים. מוליכים למחצה מסוג N הם חיוניים בייצור התקנים הדורשים אלקטרונים כנושאי מטען עיקריים, כגון התקני כוח מסוימים. (2) מוליך למחצה מסוג P: כאשר יסודות טומאה תלת-ערכיים כמו בורון (B), גליום (Ga) או אינדיום (In) מוכנסים למוליך למחצה סיליקון, אלקטרוני הערכיות של אטומי הטומאה יוצרים קשרים קוולנטיים עם אטומי הסיליקון הסובבים אותם, אך חסר להם לפחות אלקטרון ערכיות אחד ואינם יכולים ליצור קשר קוולנטי מלא. זה מוביל לריכוז חורים גדול מריכוז האלקטרונים, ויוצר מוליך למחצה מסוג P, המכונה גם מוליך למחצה מסוג חור. מוליכים למחצה מסוג P ממלאים תפקיד מפתח בייצור התקנים שבהם חורים משמשים כנושאי המטען העיקריים, כגון דיודות וטרנזיסטורים מסוימים.
התנגדות: התנגדות היא גודל פיזיקלי מרכזי המודד את המוליכות החשמלית של פרוסות סיליקון גבישיות מלוטשות. ערכה משקף את ביצועי ההולכה של החומר. ככל שההתנגדות נמוכה יותר, כך המוליכות של פרוסת הסיליקון טובה יותר; לעומת זאת, ככל שההתנגדות גבוהה יותר, כך המוליכות ירודה יותר. ההתנגדות של פרוסות סיליקון נקבעת על ידי תכונות החומר הטבועות בהן, וגם לטמפרטורה יש השפעה משמעותית. באופן כללי, ההתנגדות של פרוסות סיליקון עולה עם הטמפרטורה. ביישומים מעשיים, להתקנים מיקרואלקטרוניים שונים יש דרישות התנגדות שונות עבור פרוסות סיליקון. לדוגמה, פרוסות סיליקון המשמשות בייצור מעגלים משולבים זקוקות לשליטה מדויקת בהתנגדות כדי להבטיח ביצועי התקן יציבים ואמינים.
כיוון: כיוון הגביש של פרוסת הסיליקון מייצג את הכיוון הקריסטלוגרפי של סריג הסיליקון, המצוין בדרך כלל על ידי מדדי מילר כגון (100), (110), (111) וכו'. לכיווני גביש שונים יש תכונות פיזיקליות שונות, כגון צפיפות הקווים, המשתנה בהתאם לכיוון. הבדל זה יכול להשפיע על ביצועי פרוסת הסיליקון בשלבי העיבוד הבאים ועל הביצועים הסופיים של התקנים מיקרואלקטרוניים. בתהליך הייצור, בחירת פרוסת סיליקון עם הכיוון המתאים לדרישות התקן שונות יכולה לייעל את ביצועי המכשיר, לשפר את יעילות הייצור ולשפר את איכות המוצר.
שטוח/חריץ: הקצה השטוח (Flat) או החריץ V (Notch) על היקף פרוסת הסיליקון ממלא תפקיד קריטי ביישור כיוון הגביש והוא מזהה חשוב בייצור ובעיבוד של פרוסת הסיליקון. פרוסות בקטרים שונים תואמות לתקנים שונים לאורך ה-Flat או החריץ. קצוות היישור מסווגים ל-Flat ראשוני ול-Flat משני. ה-Flat הראשוני משמש בעיקר לקביעת כיוון הגביש הבסיסי וייחוס העיבוד של הפרוסת הסיליקון, בעוד שה-Flat המשני מסייע עוד יותר ביישור ועיבוד מדויקים, ומבטיח פעולה מדויקת ועקביות של הפרוסת הסיליקון לאורך כל קו הייצור.
עובי: עובי פרוסה מוגדר בדרך כלל במיקרומטרים (מיקרומטר), כאשר עוביים נפוצים נע בין 100 מיקרומטר ל-1000 מיקרומטר. פרוסות בעוביים שונים מתאימות לסוגים שונים של התקנים מיקרואלקטרוניים. פרוסות דקות יותר (למשל, 100 מיקרומטר - 300 מיקרומטר) משמשות לעתים קרובות לייצור שבבים הדורש בקרת עובי קפדנית, מה שמפחית את גודל ומשקל השבב ומגדיל את צפיפות האינטגרציה. פרוסות עבות יותר (למשל, 500 מיקרומטר - 1000 מיקרומטר) נמצאות בשימוש נרחב במכשירים הדורשים חוזק מכני גבוה יותר, כגון התקני מוליכים למחצה להספק, כדי להבטיח יציבות במהלך הפעולה.
חספוס פני השטח: חספוס פני השטח הוא אחד הפרמטרים המרכזיים להערכת איכות פרוסת הוואפל, מכיוון שהוא משפיע ישירות על ההידבקות בין הפרוסה לחומרי שכבה דקה המופקדים לאחר מכן, כמו גם על הביצועים החשמליים של המכשיר. חספוס פני השטח מבוטא בדרך כלל כחספוס שורש ממוצע הריבועים (RMS) (בננומטרים). חספוס פני השטח נמוך יותר פירושו שפני הפרוסה חלקים יותר, מה שעוזר להפחית תופעות כמו פיזור אלקטרונים ומשפר את ביצועי המכשיר ואמינותו. בתהליכי ייצור מתקדמים של מוליכים למחצה, דרישות חספוס פני השטח הופכות מחמירות יותר ויותר, במיוחד עבור ייצור מעגלים משולבים מתקדמים, שבהם יש לשלוט בחספוס פני השטח לכמה ננומטרים או אפילו נמוך יותר.
וריאציה כוללת של עובי (TTV): וריאציה כוללת של עובי מתייחסת להבדל בין העוביים המקסימלי והמינימלי הנמדד בנקודות מרובות על פני השטח של פרוסת הוופל, מבוטא בדרך כלל במיקרומטר. TTV גבוה עלול להוביל לסטיות בתהליכים כגון פוטוליוגרפיה ותחריט, דבר המשפיע על עקביות ביצועי המכשיר ועל התפוקה. לכן, בקרת TTV במהלך ייצור פרוסת הוופל היא צעד מפתח בהבטחת איכות המוצר. עבור ייצור התקנים מיקרואלקטרוניים בדיוק גבוה, TTV נדרש בדרך כלל להיות בטווח של כמה מיקרומטרים.
קשת: קשת מתייחסת לסטייה בין פני השטח של פרוסת המזון למישור השטוח האידיאלי, הנמדדת בדרך כלל במיקרומטר. פרוסות עם קשת מוגזמת עלולות להישבר או לחוות עומס לא אחיד במהלך העיבוד שלאחר מכן, דבר המשפיע על יעילות הייצור ואיכות המוצר. במיוחד בתהליכים הדורשים שטוחות גבוהה, כגון פוטוליוגרפיה, יש לשלוט בקשת בטווח מסוים כדי להבטיח את הדיוק והעקביות של התבנית הפוטוליוגרפית.
עיוות: עיוות מציין את הסטייה בין פני השטח של הוופל לצורה הכדורית האידיאלית, הנמדדת גם היא במיקרומטר. בדומה לקשת, עיוות הוא אינדיקטור חשוב לשטיחות הוופל. עיוות מוגזם לא רק משפיע על דיוק המיקום של הוופל בציוד עיבוד, אלא גם יכול לגרום לבעיות במהלך תהליך אריזת השבב, כגון חיבור לקוי בין השבב לחומר האריזה, מה שמשפיע בתורו על אמינות ההתקן. בייצור מוליכים למחצה מתקדמים, דרישות העיוות הופכות מחמירות יותר כדי לעמוד בדרישות של תהליכי ייצור ואריזה מתקדמים של שבבים.
פרופיל קצה: פרופיל הקצה של פרוסת סיליקון הוא קריטי לעיבוד ולטיפול שלה לאחר מכן. הוא מוגדר בדרך כלל על ידי אזור אי הכללת הקצה (EEZ), המגדיר את המרחק מקצה הפרוסת הסיליקון שבו אין עיבוד. פרופיל קצה שתוכנן כראוי ובקרת EEZ מדויקת מסייעים במניעת פגמי קצה, ריכוזי מאמץ ובעיות אחרות במהלך העיבוד, ומשפרים את איכות הפרוסת הסיליקון הכוללת ואת התפוקה. בתהליכי ייצור מתקדמים מסוימים, נדרש דיוק של פרופיל הקצה ברמה תת-מיקרון.
ספירת חלקיקים: מספר החלקיקים ופיזורם הגודל על פני הוופל משפיעים באופן משמעותי על ביצועי התקנים מיקרואלקטרוניים. חלקיקים מוגזמים או גדולים עלולים להוביל לכשלים במכשיר, כגון קצר חשמלי או דליפה, מה שמפחית את תפוקת המוצר. לכן, ספירת החלקיקים נמדדת בדרך כלל על ידי ספירת החלקיקים ליחידת שטח, כגון מספר החלקיקים הגדולים מ-0.3 מיקרומטר. בקרה קפדנית על ספירת החלקיקים במהלך ייצור הוופל היא מדד חיוני להבטחת איכות המוצר. טכנולוגיות ניקוי מתקדמות וסביבת ייצור נקייה משמשות כדי למזער את זיהום החלקיקים על פני הוופל.
הפקה קשורה
פרוסת סיליקון גבישית יחידה Si מצע סוג N/P פרוסת סיליקון קרביד אופציונלית
פרוסת סיליקון FZ CZ Si במלאי פרוסת סיליקון 12 אינץ', בדיקה או בדיקה
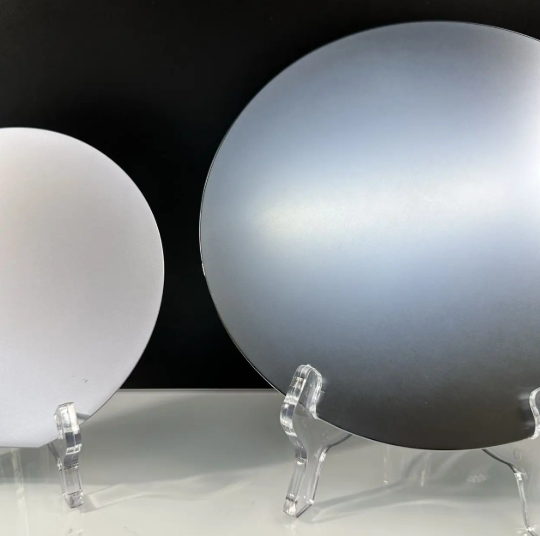
זמן פרסום: 18 באפריל 2025