טכנולוגיית חיתוך פרוסות ופלים, כשלב קריטי בתהליך ייצור מוליכים למחצה, קשורה ישירות לביצועי השבב, לתפוקה ולעלויות הייצור.
#01 רקע ומשמעות של חיתוך פרוסות ופל
1.1 הגדרת חיתוך פרוסות
חיתוך פרוסות ופלים (הידועה גם בשם scribing) הוא שלב חיוני בייצור מוליכים למחצה, שמטרתו לחלק פרוסות ופלים מעובדות למספר שבבים בודדים. שבבים אלה מכילים בדרך כלל פונקציונליות מעגל מלאה והם הרכיבים המרכזיים המשמשים בסופו של דבר בייצור מכשירים אלקטרוניים. ככל שתכנון השבבים הופך מורכב יותר והממדים ממשיכים להתכווץ, דרישות הדיוק והיעילות לטכנולוגיית חיתוך פרוסות ופלים הופכות מחמירות יותר ויותר.
בפעולות מעשיות, חיתוך פרוסות ופלים משתמש בדרך כלל בכלים מדויקים כמו להבי יהלום כדי להבטיח שכל תבנית תישאר שלמה ותפקודית לחלוטין. שלבים מרכזיים כוללים הכנה לפני החיתוך, בקרה מדויקת במהלך תהליך החיתוך ובדיקת איכות לאחר החיתוך.
לפני החיתוך, יש לסמן ולמקם את הוופל כדי להבטיח נתיבי חיתוך מדויקים. במהלך החיתוך, יש לשלוט בקפדנות בפרמטרים כגון לחץ הכלי ומהירות כדי למנוע נזק לוופל. לאחר החיתוך, נערכות בדיקות איכות מקיפות כדי להבטיח שכל שבב עומד בתקני הביצועים.
העקרונות הבסיסיים של טכנולוגיית חיתוך פרוסות סיליקון (wafers) כוללים לא רק את בחירת ציוד החיתוך וקביעת פרמטרי התהליך, אלא גם את השפעת התכונות המכניות והמאפיינים של החומרים על איכות החיתוך. לדוגמה, פרוסות סיליקון דיאלקטריות בעלות רמת k נמוכה (low-k), בשל תכונותיהן המכניות הנחותות, רגישות מאוד לריכוז מאמצים במהלך החיתוך, מה שמוביל לכשלים כמו סדקים וקשיחות. הקשיות והשבירות הנמוכות של חומרים בעלי רמת k נמוכה הופכות אותם מועדים יותר לנזק מבני תחת כוח מכני או מאמצים תרמיים, במיוחד במהלך חיתוך. המגע בין הכלי לפני השטח של הפרוסה, בשילוב עם טמפרטורות גבוהות, יכול להחריף עוד יותר את ריכוז המאמצים.
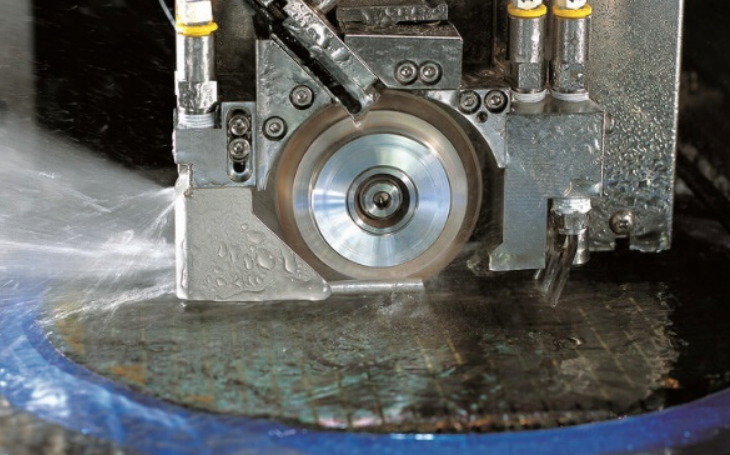
עם ההתקדמות במדעי החומרים, טכנולוגיית חיתוך פרוסות סיליקון התרחבה מעבר למוליכים למחצה מסורתיים מבוססי סיליקון וכללה חומרים חדשים כמו גליום ניטריד (GaN). חומרים חדשים אלה, בשל קשיותם ותכונותיהם המבניות, מציבים אתגרים חדשים לתהליכי חיתוך, המחייבים שיפורים נוספים בכלי חיתוך ובטכניקות.
כתהליך קריטי בתעשיית המוליכים למחצה, חיתוך פרוסות ופלים (wafer dicing) ממשיך להיות אופטימיזציה בתגובה לדרישות מתפתחות ולהתקדמות טכנולוגית, ומניח את היסודות לטכנולוגיות מיקרואלקטרוניקה ומעגלים משולבים עתידיות.
שיפורים בטכנולוגיית חיתוך פרוסות ופלים חורגים מעבר לפיתוח חומרים וכלים נלווים. הם כוללים גם אופטימיזציה של תהליכים, שיפורים בביצועי הציוד ובקרה מדויקת על פרמטרי החיתוך. התקדמויות אלו נועדו להבטיח דיוק, יעילות ויציבות גבוהים בתהליך חיתוך פרוסות הופלים, תוך מענה לצורך של תעשיית המוליכים למחצה בממדים קטנים יותר, אינטגרציה גבוהה יותר ומבני שבבים מורכבים יותר.
אזור שיפור | אמצעים ספציפיים | אפקטים |
אופטימיזציה של תהליכים | - שיפור ההכנות הראשוניות, כגון מיקום פרוסות מדויק יותר ותכנון נתיב. | - צמצום שגיאות חיתוך ושיפור היציבות. |
- מזעור שגיאות חיתוך ושיפור היציבות. | - אימוץ מנגנוני ניטור ומשוב בזמן אמת כדי להתאים את לחץ הכלי, המהירות והטמפרטורה. | |
- שיעורי שבירת פרוסות פרוסות נמוכים יותר ושיפור איכות השבב. | ||
שיפור ביצועי הציוד | - שימוש במערכות מכניות מדויקות ובטכנולוגיית בקרה אוטומטיבית מתקדמת. | - שיפור דיוק החיתוך והפחתת בזבוז חומרים. |
- להציג טכנולוגיית חיתוך לייזר המתאימה לפלים מחומרים קשים במיוחד. | - שיפור יעילות הייצור והפחתת טעויות ידניות. | |
- הגברת אוטומציה של הציוד לצורך ניטור והתאמות אוטומטיות. | ||
בקרת פרמטרים מדויקת | - כוונון דק של פרמטרים כמו עומק חיתוך, מהירות, סוג הכלי ושיטות קירור. | - ודא שלמות השבב וביצועים חשמליים. |
- התאמה אישית של פרמטרים בהתבסס על חומר, עובי ומבנה פרוסת הוופל. | - הגברת שיעורי התפוקה, הפחתת בזבוז חומרים והורדת עלויות ייצור. | |
משמעות אסטרטגית | - לחקור באופן מתמיד נתיבים טכנולוגיים חדשים, לייעל תהליכים ולשפר את יכולות הציוד כדי לעמוד בדרישות השוק. | - שיפור תפוקה וביצועי ייצור שבבים, תמיכה בפיתוח חומרים חדשים ועיצובי שבבים מתקדמים. |
1.2 חשיבות חיתוך הוופלים
חיתוך פרוסות (wafer dicing) ממלא תפקיד קריטי בתהליך ייצור המוליכים למחצה, ומשפיע ישירות על השלבים הבאים וכן על האיכות והביצועים של המוצר הסופי. ניתן לפרט את חשיבותו כדלקמן:
ראשית, הדיוק והעקביות של החיתוך הם המפתח להבטחת תפוקת השבב ואמינותו. במהלך הייצור, פרוסות סיליקון עוברות שלבי עיבוד מרובים כדי ליצור מבני מעגלים מורכבים רבים, אשר חייבים להיות מחולקים במדויק לשבבים (דיס) בודדים. אם ישנן שגיאות משמעותיות ביישור או בחיתוך במהלך תהליך החיתוך, המעגלים עלולים להינזק, מה שמשפיע על פונקציונליות השבב ואמינותו. לכן, טכנולוגיית חיתוך מדויקת במיוחד לא רק מבטיחה את שלמותו של כל שבב אלא גם מונעת נזק למעגלים פנימיים, ומשפרת את שיעור התפוקה הכולל.
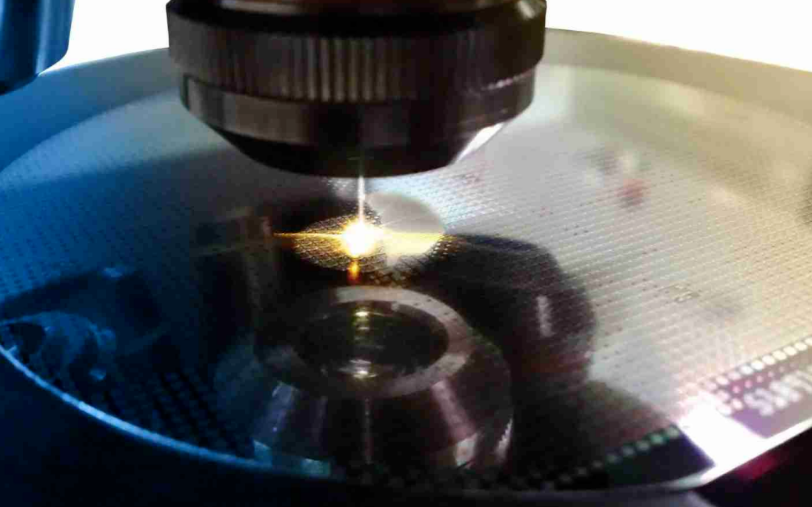
שנית, חיתוך פרוסות ופלים משפיע באופן משמעותי על יעילות הייצור ובקרת העלויות. כשלב מכריע בתהליך הייצור, יעילותו משפיעה ישירות על התקדמות השלבים הבאים. על ידי אופטימיזציה של תהליך החיתוך, הגדלת רמות האוטומציה ושיפור מהירויות החיתוך, ניתן לשפר משמעותית את יעילות הייצור הכוללת.
מצד שני, בזבוז חומרים במהלך חיתוך הוא גורם קריטי בניהול עלויות. שימוש בטכנולוגיות חיתוך מתקדמות לא רק מפחית אובדן חומר מיותרים במהלך תהליך החיתוך, אלא גם מגביר את ניצול הפרוסות, ובכך מוריד את עלויות הייצור.
עם ההתקדמות בטכנולוגיית המוליכים למחצה, קוטר פרוסות החיתוך ממשיכים לגדול, וצפיפויות המעגלים עולות בהתאם, מה שמציב דרישות גבוהות יותר לטכנולוגיית חיתוך. פרוסות חיתוך גדולות יותר דורשות שליטה מדויקת יותר בנתיבי החיתוך, במיוחד באזורים בעלי צפיפות מעגלים גבוהה, שבהם אפילו סטיות קלות עלולות לגרום לפגמים בשבבים מרובים. בנוסף, פרוסות חיתוך גדולות יותר כרוכות ביותר קווי חיתוך ושלבי תהליך מורכבים יותר, מה שמצריך שיפורים נוספים בדיוק, בעקביות וביעילות של טכנולוגיות חיתוך חיתוך כדי לעמוד באתגרים אלה.
1.3 תהליך חיתוך פרוסות פרוסות
תהליך חיתוך הוופלים כולל את כל השלבים, החל משלב ההכנה ועד לבדיקת האיכות הסופית, כאשר כל שלב הוא קריטי להבטחת האיכות והביצועים של השבבים החתוכים לקוביות. להלן הסבר מפורט על כל שלב.
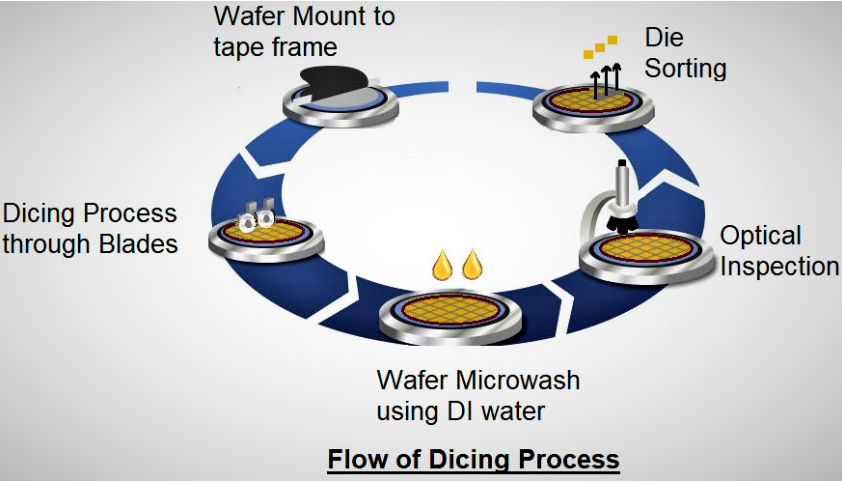
שָׁלָב | תיאור מפורט |
שלב ההכנה | -ניקוי ופליםהשתמשו במים בעלי טוהר גבוה ובחומרי ניקוי מיוחדים, בשילוב עם קרצוף אולטרסאונד או מכני, כדי להסיר זיהומים, חלקיקים ומזהמים, ולהבטיח משטח נקי. -מיקום מדויקהשתמשו בציוד מדויק כדי להבטיח שהפרוסה מחולקת במדויק לאורך נתיבי החיתוך שתוכננו. -קיבוע פרוסותיש לאבטח את הוופל על מסגרת סרט כדי לשמור על יציבות במהלך החיתוך, ולמנוע נזק מרעידות או תנועה. |
שלב החיתוך | -חיתוך להבשימוש בלהבים מסתובבים במהירות גבוהה מצופים יהלום לחיתוך פיזי, מתאים לחומרים מבוססי סיליקון וחסכוני. -חיתוך בלייזרשימוש בקרני לייזר בעלות אנרגיה גבוהה לחיתוך ללא מגע, אידיאלי לחומרים שבירים או בעלי קשיות גבוהה כמו גליום ניטריד, המציע דיוק גבוה יותר ופחות אובדן חומר. -טכנולוגיות חדשותהכנסת טכנולוגיות חיתוך לייזר ופלזמה לשיפור נוסף של היעילות והדיוק תוך מזעור אזורים מושפעי חום. |
שלב הניקוי | - השתמשו במים מזוקקים (מים DI) ובחומרי ניקוי ייעודיים, בשילוב עם ניקוי באולטרסאונד או בהתזה, כדי להסיר פסולת ואבק שנוצרים במהלך החיתוך, ולמנוע משאריות להשפיע על תהליכים עתידיים או על הביצועים החשמליים של השבב. - מים DI בעלי טוהר גבוה מונעים החדרת מזהמים חדשים, ומבטיחים סביבת ופלים נקייה. |
שלב הבדיקה | -בדיקה אופטיתהשתמשו במערכות גילוי אופטיות בשילוב עם אלגוריתמים של בינה מלאכותית כדי לזהות במהירות פגמים, להבטיח שאין סדקים או סדקים בקוביות השבבים, לשפר את יעילות הבדיקה ולהפחית טעויות אנוש. -מדידת ממדודא שמידות השבב עומדות במפרטי התכנון. -בדיקות ביצועים חשמליותלהבטיח שהביצועים החשמליים של שבבים קריטיים עומדים בתקנים, תוך הבטחת אמינות ביישומים עתידיים. |
שלב המיון | - השתמשו בזרועות רובוטיות או בכוסות יניקה של ואקום כדי להפריד שבבים מתאימים ממסגרת הסרט ולמיין אותם באופן אוטומטי על סמך ביצועים, תוך הבטחת יעילות וגמישות ייצור תוך שיפור הדיוק. |
תהליך חיתוך פרוסות ה-Wraps כולל ניקוי, מיקום, חיתוך, ניקוי, בדיקה ומיון של פרוסות, כאשר כל שלב הוא קריטי. עם ההתקדמות באוטומציה, חיתוך לייזר וטכנולוגיות בדיקה מבוססות בינה מלאכותית, מערכות חיתוך פרוסות מודרניות יכולות להשיג דיוק, מהירות ואובדן חומר נמוך יותר. בעתיד, טכנולוגיות חיתוך חדשות כמו לייזר ופלזמה יחליפו בהדרגה את חיתוך הלהב המסורתי כדי לענות על הצרכים של עיצובי שבבים מורכבים יותר ויותר, ויניעו עוד יותר את פיתוח תהליכי ייצור המוליכים למחצה.
טכנולוגיית חיתוך פרוסות ועקרונותיה
התמונה ממחישה שלוש טכנולוגיות נפוצות לחיתוך ופלים:חיתוך להב,חיתוך בלייזר, וחיתוך פלזמהלהלן ניתוח מפורט והסבר משלים של שלוש הטכניקות הללו:
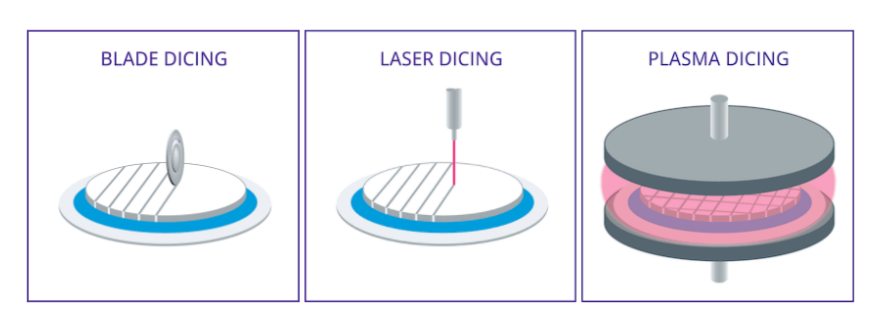
בייצור מוליכים למחצה, חיתוך פרוסות סיליקון הוא שלב מכריע הדורש בחירת שיטת החיתוך המתאימה בהתבסס על עובי הפרוסה. השלב הראשון הוא קביעת עובי הפרוסה. אם עובי הפרוסה עולה על 100 מיקרון, ניתן לבחור בשיטת חיתוך להב כשיטת החיתוך. אם חיתוך להב אינו מתאים, ניתן להשתמש בשיטת חיתוך שבר, הכוללת גם טכניקות חיתוך חריץ וגם טכניקות חיתוך להב.
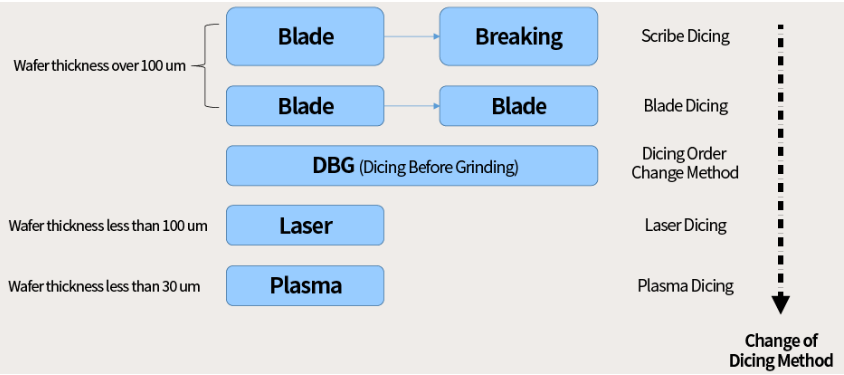
כאשר עובי הפרוסה הוא בין 30 ל-100 מיקרון, מומלצת שיטת DBG (Dice Before Grinding). במקרה זה, ניתן לבחור בחיתוך חריץ, חיתוך להב או התאמת רצף החיתוך לפי הצורך כדי להשיג את התוצאות הטובות ביותר.
עבור פרוסות ופלים דקים במיוחד בעובי של פחות מ-30 מיקרון, חיתוך בלייזר הופך לשיטה המועדפת בשל יכולתו לחתוך פרוסות דקות בצורה מדויקת מבלי לגרום נזק מוגזם. אם חיתוך בלייזר אינו יכול לעמוד בדרישות ספציפיות, ניתן להשתמש בחיתוך בפלזמה כחלופה. תרשים זרימה זה מספק נתיב קבלת החלטות ברור כדי להבטיח בחירת טכנולוגיית חיתוך הפרוסות המתאימה ביותר בתנאי עובי שונים.
2.1 טכנולוגיית חיתוך מכנית
טכנולוגיית חיתוך מכנית היא השיטה המסורתית בחיתוך פרוסות פרוסות. העיקרון המרכזי הוא שימוש בגלגל השחזה יהלום מסתובב במהירות גבוהה ככלי חיתוך לחיתוך הוופל. הציוד המרכזי כולל ציר בעל נושא אוויר, המניע את כלי השחזה של גלגל היהלום במהירויות גבוהות כדי לבצע חיתוך או חריצים מדויקים לאורך נתיב חיתוך מוגדר מראש. טכנולוגיה זו נמצאת בשימוש נרחב בתעשייה בשל עלותה הנמוכה, יעילותה הגבוהה ויכולתה הרחבה.
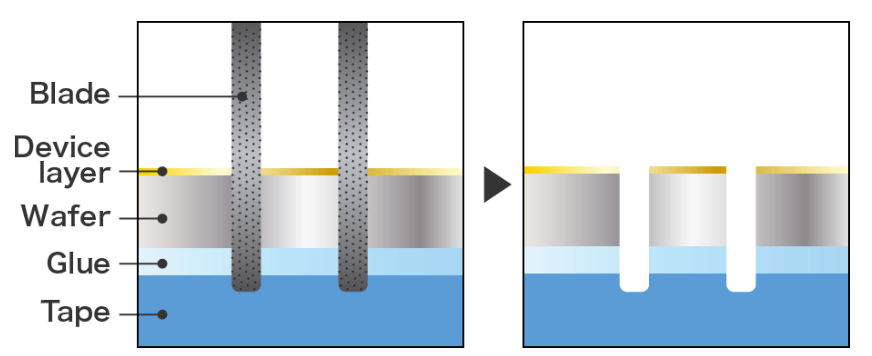
יתרונות
הקשיות הגבוהה ועמידות הבלאי של כלי גלגלי השחזה של יהלום מאפשרים לטכנולוגיית חיתוך מכני להתאים את עצמה לצורכי החיתוך של חומרי פרוסות שונים, בין אם חומרים מסורתיים מבוססי סיליקון או מוליכים למחצה מורכבים חדשים יותר. פעולתה פשוטה, עם דרישות טכניות נמוכות יחסית, מה שמקדם עוד יותר את הפופולריות שלה בייצור המוני. בנוסף, בהשוואה לשיטות חיתוך אחרות כמו חיתוך בלייזר, לחיתוך מכני יש עלויות נשלטות יותר, מה שהופך אותו מתאים לצורכי ייצור בנפח גבוה.
מגבלות
למרות יתרונותיה הרבים, לטכנולוגיית חיתוך מכני יש גם מגבלות. ראשית, עקב המגע הפיזי בין הכלי לפרוסת ה-wafer, דיוק החיתוך מוגבל יחסית, מה שמוביל לעתים קרובות לסטיות ממדיות שעלולות להשפיע על דיוק אריזת השבבים והבדיקות לאחר מכן. שנית, פגמים כמו סדקים וקילופים עלולים להתרחש בקלות במהלך תהליך החיתוך המכני, דבר שמשפיע לא רק על שיעור התפוקה אלא גם על אמינותם ועל תוחלת החיים של השבבים. הנזק הנגרם ממאמץ מכני מזיק במיוחד לייצור שבבים בצפיפות גבוהה, במיוחד בעת חיתוך חומרים שבירים, שבהם בעיות אלו בולטות יותר.
שיפורים טכנולוגיים
כדי להתגבר על מגבלות אלו, חוקרים מבצעים באופן מתמיד אופטימיזציה של תהליך החיתוך המכני. שיפורים מרכזיים כוללים שיפור התכנון ובחירת החומרים של גלגלי השחזה כדי לשפר את דיוק החיתוך והעמידות. בנוסף, אופטימיזציה של התכנון המבני ומערכות הבקרה של ציוד חיתוך שיפרה עוד יותר את היציבות והאוטומציה של תהליך החיתוך. התקדמויות אלו מצמצמות שגיאות הנגרמות על ידי פעולות אנושיות ומשפרות את עקביות החיתוכים. הכנסת טכנולוגיות בדיקה ובקרת איכות מתקדמות לניטור בזמן אמת של אנומליות במהלך תהליך החיתוך שיפרה משמעותית גם את אמינות החיתוך ואת התפוקה.
פיתוח עתידי וטכנולוגיות חדשות
למרות שטכנולוגיית חיתוך מכני עדיין תופסת מקום משמעותי בחיתוך פרוסות סיליקון, טכנולוגיות חיתוך חדשות מתקדמות במהירות ככל שתהליכי מוליכים למחצה מתפתחים. לדוגמה, יישום טכנולוגיית חיתוך לייזר תרמי מספק פתרונות חדשים לבעיות דיוק ופגמים בחיתוך מכני. שיטת חיתוך ללא מגע זו מפחיתה את הלחץ הפיזי על הפרוסה הרגילה, ומורידה משמעותית את שכיחות הסדיקה והסדקים, במיוחד בעת חיתוך חומרים שבירים יותר. בעתיד, שילוב טכנולוגיית חיתוך מכני עם טכניקות חיתוך מתקדמות יספק לייצור מוליכים למחצה אפשרויות וגמישות רבות יותר, וישפר עוד יותר את יעילות הייצור ואת איכות השבב.
לסיכום, למרות שלטכנולוגיית חיתוך מכני יש חסרונות מסוימים, שיפורים טכנולוגיים מתמשכים ושילובה עם טכניקות חיתוך חדשות מאפשרים לה עדיין למלא תפקיד חשוב בייצור מוליכים למחצה ולשמור על התחרותיות שלה בתהליכים עתידיים.
2.2 טכנולוגיית חיתוך לייזר
טכנולוגיית חיתוך לייזר, כשיטה חדשה בחיתוך פרוסות סיליקון, זכתה בהדרגה לתשומת לב נרחבת בתעשיית המוליכים למחצה בשל דיוקה הגבוה, היעדר נזק מכני ויכולות החיתוך המהירות שלה. טכנולוגיה זו משתמשת בצפיפות האנרגיה הגבוהה ויכולת המיקוד של קרן לייזר כדי ליצור אזור קטן המושפע מחום על פני חומר הפרוסות סיליקון. כאשר קרן הלייזר מופעלת על הפרוסות סיליקון, הלחץ התרמי שנוצר גורם לחומר להישבר במיקום המיועד, ובכך להשיג חיתוך מדויק.
יתרונות טכנולוגיית חיתוך לייזר
• דיוק גבוהיכולת המיקום המדויקת של קרן הלייזר מאפשרת חיתוך דיוק ברמת מיקרון או אפילו ננומטרי, ועומדת בדרישות ייצור מעגלים משולבים מודרניים בדיוק גבוה ובצפיפות גבוהה.
• ללא מגע מכניחיתוך בלייזר מונע מגע פיזי עם הוופל, מונע בעיות נפוצות בחיתוך מכני, כגון סדקים וסדיקה, ומשפר משמעותית את קצב התפוקה והאמינות של השבבים.
• מהירות חיתוך מהירההמהירות הגבוהה של חיתוך בלייזר תורמת ליעילות הייצור המוגברת, מה שהופך אותו מתאים במיוחד לתרחישי ייצור בקנה מידה גדול ובמהירות גבוהה.
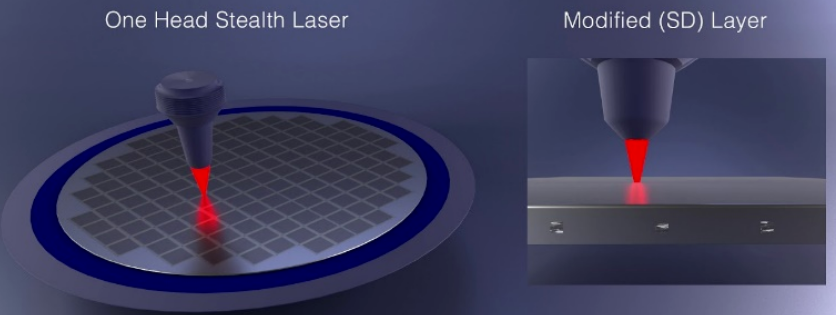
אתגרים העומדים בפנינו
• עלות ציוד גבוההההשקעה הראשונית בציוד חיתוך לייזר היא גבוהה, דבר המציב לחץ כלכלי, במיוחד עבור מפעלי ייצור קטנים ובינוניים.
• בקרת תהליכים מורכבתחיתוך בלייזר דורש שליטה מדויקת במספר פרמטרים, כולל צפיפות אנרגיה, מיקום מיקוד ומהירות חיתוך, מה שהופך את התהליך למורכב.
• בעיות באזור מושפע חוםלמרות שאופיו הלא-מגע של חיתוך בלייזר מפחית נזק מכני, הלחץ התרמי הנגרם על ידי האזור המושפע מחום (HAZ) יכול להשפיע לרעה על תכונות חומר הוופל. יש צורך באופטימיזציה נוספת של התהליך כדי למזער השפעה זו.
כיווני שיפור טכנולוגי
כדי להתמודד עם אתגרים אלה, חוקרים מתמקדים בהורדת עלויות הציוד, שיפור יעילות החיתוך ואופטימיזציה של זרימת התהליך.
• לייזרים ומערכות אופטיות יעילותעל ידי פיתוח לייזרים יעילים יותר ומערכות אופטיות מתקדמות, ניתן להפחית את עלויות הציוד תוך שיפור דיוק ומהירות החיתוך.
• אופטימיזציה של פרמטרי תהליךמחקר מעמיק על האינטראקציה בין לייזרים וחומרי ופלים מתבצע כדי לשפר תהליכים המפחיתים את האזור המושפע מחום, ובכך משפרים את איכות החיתוך.
• מערכות בקרה חכמותפיתוח טכנולוגיות בקרה חכמות שואף להפוך את תהליך חיתוך הלייזר לאוטומטי ולייעל, תוך שיפור יציבותו ועקביותו.
טכנולוגיית חיתוך בלייזר יעילה במיוחד בפרוסות דקות במיוחד ובתרחישי חיתוך מדויקים. ככל שגודל הפרוסות גדל וצפיפות המעגלים עולה, שיטות חיתוך מכניות מסורתיות מתקשות לעמוד בדרישות הדיוק והיעילות הגבוהה של ייצור מוליכים למחצה מודרני. בשל יתרונותיו הייחודיים, חיתוך בלייזר הופך לפתרון המועדף בתחומים אלה.
למרות שטכנולוגיית חיתוך הלייזר עדיין מתמודדת עם אתגרים כמו עלויות ציוד גבוהות ומורכבות התהליך, יתרונותיה הייחודיים בדיוק גבוה ובנזק ללא מגע הופכים אותה לכיוון חשוב לפיתוח בייצור מוליכים למחצה. ככל שטכנולוגיית הלייזר ומערכות הבקרה החכמות ממשיכות להתקדם, חיתוך הלייזר צפוי לשפר עוד יותר את יעילות ואיכות חיתוך פרוסות הלייזר, ולהניע את הפיתוח המתמשך של תעשיית המוליכים למחצה.
2.3 טכנולוגיית חיתוך פלזמה
טכנולוגיית חיתוך פלזמה, כשיטת חיתוך פרוסות ופלים מתפתחת, זכתה לתשומת לב רבה בשנים האחרונות. טכנולוגיה זו משתמשת בקרני פלזמה בעלות אנרגיה גבוהה לחיתוך ופלים במדויק על ידי שליטה באנרגיה, במהירות ובנתיב החיתוך של קרן הפלזמה, ובכך משיגה תוצאות חיתוך אופטימליות.
עקרון עבודה ויתרונות
תהליך חיתוך הפלזמה מסתמך על קרן פלזמה בטמפרטורה גבוהה ובאנרגיה גבוהה הנוצרת על ידי הציוד. קרן זו יכולה לחמם את חומר הוופל לנקודת ההיתוך או האידוי שלו בזמן קצר מאוד, מה שמאפשר חיתוך מהיר. בהשוואה לחיתוך מכני או לייזר מסורתי, חיתוך פלזמה מהיר יותר ומייצר אזור קטן יותר המושפע מחום, מה שמפחית ביעילות את התרחשות הסדקים והנזקים במהלך החיתוך.
ביישומים מעשיים, טכנולוגיית חיתוך פלזמה מיומנת במיוחד בטיפול בפרוסות ופלים בעלי צורות מורכבות. קרן הפלזמה המתכווננת והעוצמתית שלה יכולה לחתוך בקלות פרוסות בעלות צורה לא סדירה בדיוק רב. לכן, בייצור מיקרואלקטרוניקה, במיוחד בייצור מותאם אישית ובקבוצות קטנות של שבבים מתקדמים, טכנולוגיה זו מראה פוטנציאל רב לשימוש נרחב.
אתגרים ומגבלות
למרות היתרונות הרבים של טכנולוגיית חיתוך פלזמה, היא ניצבת גם בפני כמה אתגרים.
• תהליך מורכבתהליך חיתוך הפלזמה מורכב ודורש ציוד מדויק ומפעילים מנוסים כדי להבטיחדיוק ויציבות בחיתוך.
• בקרת סביבה ובטיחותאופייה של קרן הפלזמה, בעלת הטמפרטורה הגבוהה והאנרגיה הגבוהה, דורש אמצעי בקרה ובטיחות סביבתיים מחמירים, מה שמגדיל את המורכבות והעלות של היישום.
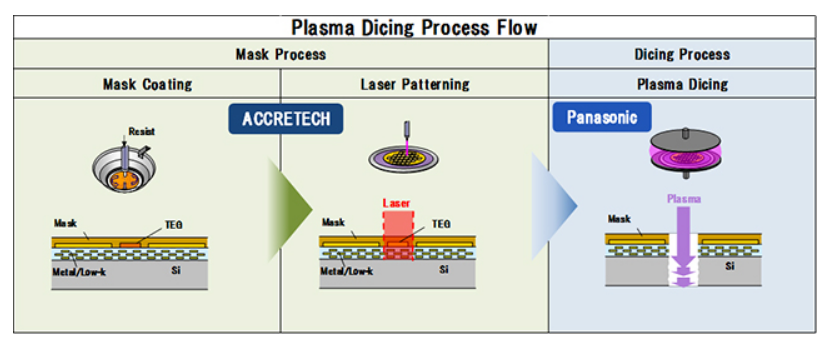
כיווני פיתוח עתידיים
עם ההתקדמות הטכנולוגית, צפוי כי האתגרים הקשורים לחיתוך בפלזמה יתגברו בהדרגה. על ידי פיתוח ציוד חיתוך חכם ויציב יותר, ניתן להפחית את התלות בפעולות ידניות, ובכך לשפר את יעילות הייצור. במקביל, אופטימיזציה של פרמטרי התהליך וסביבת החיתוך תסייע בהפחתת סיכוני הבטיחות ועלויות התפעול.
בתעשיית המוליכים למחצה, חידושים בטכנולוגיית חיתוך וקוביות של פרוסות ופלים הם קריטיים להנעת התפתחות התעשייה. טכנולוגיית חיתוך פלזמה, עם דיוקה הגבוה, יעילותה ויכולתה להתמודד עם צורות פרוסות מורכבות, צצה כשחקן משמעותי חדש בתחום זה. למרות שנותרו כמה אתגרים, סוגיות אלו יטופלו בהדרגה עם המשך החדשנות הטכנולוגית, שתביא אפשרויות והזדמנויות נוספות לייצור מוליכים למחצה.
סיכויי היישום של טכנולוגיית חיתוך פלזמה הם עצומים, וצפוי שהיא תמלא תפקיד חשוב יותר בייצור מוליכים למחצה בעתיד. באמצעות חדשנות טכנולוגית מתמשכת ואופטימיזציה, חיתוך פלזמה לא רק יטפל באתגרים הקיימים אלא גם יהפוך למניע רב עוצמה לצמיחת תעשיית המוליכים למחצה.
2.4 איכות החיתוך וגורמים משפיעים
איכות חיתוך פרוסות פרוסות היא קריטית לאריזת השבבים, לבדיקות ולביצועים והאמינות הכוללים של המוצר הסופי. בעיות נפוצות שנתקלות בהן במהלך חיתוך כוללות סדקים, סדקים וסטיות חיתוך. בעיות אלו מושפעות ממספר גורמים הפועלים יחד.
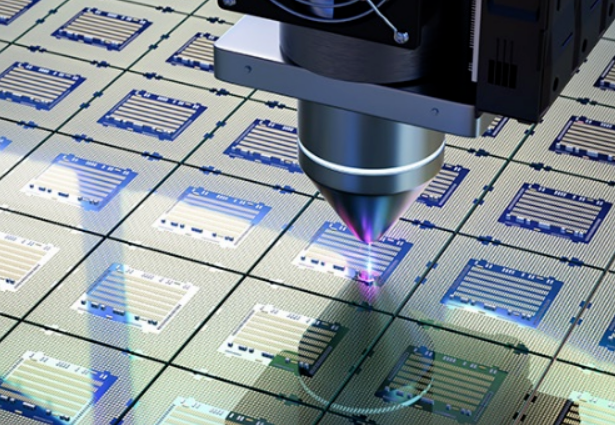
קָטֵגוֹרִיָה | תוֹכֶן | פְּגִיעָה |
פרמטרי תהליך | מהירות חיתוך, קצב הזנה ועומק חיתוך משפיעים ישירות על היציבות והדיוק של תהליך החיתוך. הגדרות לא נכונות עלולות להוביל לריכוז מאמץ ולאזור מושפע חום מוגזם, וכתוצאה מכך לסדקים וקילופים. התאמת פרמטרים מתאימה בהתבסס על חומר הפרוסה, עוביה ודרישות החיתוך היא המפתח להשגת תוצאות החיתוך הרצויות. | פרמטרי התהליך הנכונים מבטיחים חיתוך מדויק ומפחיתים את הסיכון לפגמים כמו סדקים וסדיקות. |
גורמי ציוד וחומרים | -איכות הלהבהחומר, הקשיות ועמידות הבלאי של הלהב משפיעים על חלקות תהליך החיתוך ועל שטוחות משטח החיתוך. להבים באיכות ירודה מגבירים את החיכוך והלחץ התרמי, מה שעלול להוביל לסדקים או סדקים. בחירת חומר הלהב הנכון היא קריטית. -ביצועי נוזל קירורנוזלי קירור מסייעים בהפחתת טמפרטורת החיתוך, במזעור החיכוך ובפינוי פסולת. נוזל קירור לא יעיל עלול להוביל לטמפרטורות גבוהות ולהצטברות פסולת, דבר המשפיע על איכות החיתוך ויעילותו. בחירת נוזלי קירור יעילים וידידותיים לסביבה היא חיונית. | איכות הלהב משפיעה על דיוק החיתוך וחלקותו. נוזל קירור לא יעיל עלול לגרום לאיכות ויעילות חיתוך ירודות, מה שמדגיש את הצורך בשימוש אופטימלי בנוזל קירור. |
בקרת תהליכים ובדיקת איכות | -בקרת תהליכיםניטור בזמן אמת והתאמה של פרמטרי חיתוך מרכזיים כדי להבטיח יציבות ועקביות בתהליך החיתוך. -בדיקת איכותבדיקות מראה לאחר החיתוך, מדידות ממדים ובדיקות ביצועים חשמליים מסייעות בזיהוי ולטפל בבעיות איכות במהירות, ובכך משפרות את דיוק החיתוך והעקביות. | בקרת תהליך נאותה ובדיקת איכות מסייעות להבטיח תוצאות חיתוך עקביות ואיכותיות וזיהוי מוקדם של בעיות פוטנציאליות. |

שיפור איכות החיתוך
שיפור איכות החיתוך דורש גישה מקיפה שלוקחת בחשבון פרמטרי תהליך, בחירת ציוד וחומרים, בקרת תהליכים ובדיקה. על ידי שיפור מתמיד של טכנולוגיות חיתוך ואופטימיזציה של שיטות תהליך, ניתן לשפר עוד יותר את הדיוק והיציבות של חיתוך פרוסות סיליקון, ולספק תמיכה טכנית אמינה יותר לתעשיית ייצור המוליכים למחצה.
#03 טיפול ובדיקה לאחר חיתוך
3.1 ניקוי וייבוש
שלבי הניקוי והייבוש לאחר חיתוך פרוסות סיליקון (waples) הם קריטיים להבטחת איכות השבב ולהתקדמות חלקה של התהליכים הבאים. בשלב זה, חיוני להסיר ביסודיות שאריות סיליקון, שאריות נוזל קירור ומזהמים אחרים שנוצרים במהלך החיתוך. חשוב באותה מידה לוודא שהשבבים לא ניזוקו במהלך תהליך הניקוי, ולאחר הייבוש, לוודא שלא נותרת לחות על פני השבב כדי למנוע בעיות כגון קורוזיה או פריקה אלקטרוסטטית.
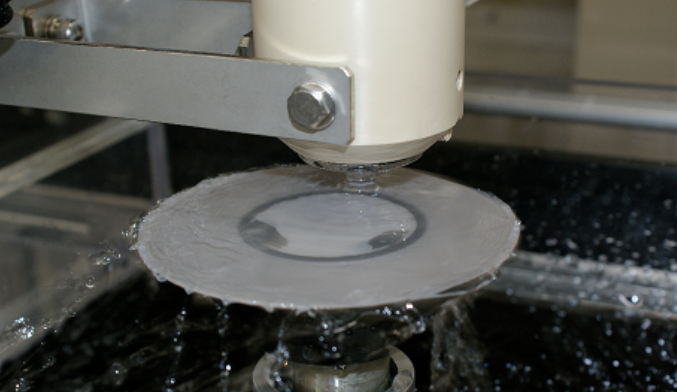
טיפול לאחר חיתוך: תהליך ניקוי וייבוש
שלב התהליך | תוֹכֶן | פְּגִיעָה |
תהליך הניקוי | -שִׁיטָההשתמשו בחומרי ניקוי ייעודיים ובמים טהורים, בשילוב עם טכניקות צחצוח אולטרסאונד או מכניות לניקוי. | מבטיח הסרה יסודית של מזהמים ומונע נזק לשבבים במהלך הניקוי. |
-בחירת חומר ניקויבחר בהתאם לחומר הוופל וסוג המזהם כדי להבטיח ניקוי יעיל מבלי לפגוע בשבב. | בחירת חומר ניקוי נכון היא המפתח לניקוי יעיל ולהגנה מפני שבבים. | |
-בקרת פרמטריםיש לשלוט בקפדנות בטמפרטורת הניקוי, בזמן ובריכוז תמיסת הניקוי כדי למנוע בעיות איכות הנגרמות מניקוי לקוי. | בקרות מסייעות למנוע נזק לוופל או השארת מזהמים מאחור, ומבטיחות איכות עקבית. | |
תהליך ייבוש | -שיטות מסורתיותייבוש טבעי באוויר וייבוש באוויר חם, אשר יעילותם נמוכה ויכולים להוביל להצטברות חשמל סטטי. | עלול לגרום לזמני ייבוש איטיים יותר ולבעיות חשמל סטטיות אפשריות. |
-טכנולוגיות מודרניותהשתמשו בטכנולוגיות מתקדמות כגון ייבוש בוואקום וייבוש אינפרא אדום כדי להבטיח שהשבבים יתייבשו במהירות וימנעו השפעות מזיקות. | תהליך ייבוש מהיר ויעיל יותר, המפחית את הסיכון לפריקה סטטית או בעיות הקשורות לחות. | |
בחירת ציוד ותחזוקה | -בחירת ציודמכונות ניקוי וייבוש בעלות ביצועים גבוהים משפרות את יעילות העיבוד ושולטות בקפידה בבעיות פוטנציאליות במהלך הטיפול. | מכונות איכותיות מבטיחות עיבוד טוב יותר ומפחיתות את הסבירות לטעויות במהלך הניקוי והייבוש. |
-תחזוקת ציודבדיקה ותחזוקה שוטפות של הציוד מבטיחות שהוא יישאר במצב עבודה אופטימלי, ומבטיחות את איכות השבב. | תחזוקה נאותה מונעת תקלות בציוד, ומבטיחה עיבוד אמין ואיכותי. |
ניקוי וייבוש לאחר חיתוך
שלבי הניקוי והייבוש לאחר חיתוך פרוסות סיליקון הם תהליכים מורכבים ועדינים הדורשים שיקול דעת מדוקדק של גורמים מרובים כדי להבטיח את תוצאת העיבוד הסופית. באמצעות שיטות מדעיות ונהלים קפדניים, ניתן להבטיח שכל שבב ייכנס לשלבי האריזה והבדיקה הבאים במצב אופטימלי.
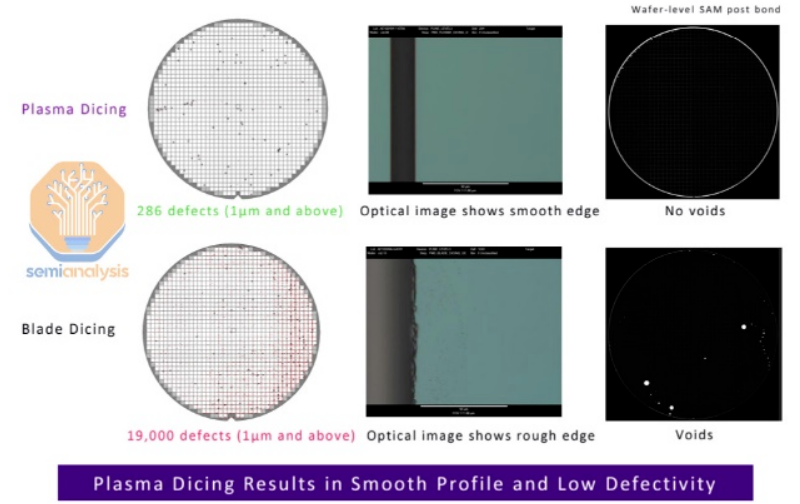
בדיקה ובדיקה לאחר חיתוך
שָׁלָב | תוֹכֶן | פְּגִיעָה |
שלב הבדיקה | 1.בדיקה חזותיתהשתמשו בציוד בדיקה חזותי או אוטומטי כדי לבדוק פגמים גלויים כמו סדקים, סדקים או זיהום על פני השבב. זהו במהירות שבבים שניזוקו פיזית כדי למנוע בזבוז. | מסייע בזיהוי וסילוק שבבים פגומים בשלב מוקדם של התהליך, תוך הפחתת אובדן חומר. |
2.מדידת גודלהשתמשו במכשירי מדידה מדויקים כדי למדוד במדויק את מידות השבב, תוך הבטחה שגודל החיתוך עומד במפרטי התכנון ומניעת בעיות ביצועים או קשיי אריזה. | מבטיח שהשבבים נמצאים במסגרת הגודל הנדרש, ומונע פגיעה בביצועים או בעיות הרכבה. | |
3.בדיקות ביצועים חשמליותהערכת פרמטרים חשמליים מרכזיים כגון התנגדות, קיבול והשראות, כדי לזהות שבבים שאינם תואמים ולהבטיח שרק שבבים בעלי ביצועים מתאימים ימשיכו לשלב הבא. | מבטיח שרק שבבים פונקציונליים ונבדקו ביצועים יתקדמו בתהליך, מה שמפחית את הסיכון לכשל בשלבים מאוחרים יותר. | |
שלב הבדיקה | 1.בדיקות פונקציונליותודא שהפונקציונליות הבסיסית של השבב פועלת כמתוכנן, זיהוי ופתרון שבבים עם ליקויים תפקודיים. | מוודא שהשבבים עומדים בדרישות התפעול הבסיסיות לפני שהם עוברים לשלבים מאוחרים יותר. |
2.בדיקות אמינותהערכת יציבות ביצועי השבב תחת שימוש ממושך או סביבות קשות, הכוללות בדרך כלל הזדקנות בטמפרטורה גבוהה, בדיקות בטמפרטורה נמוכה ובדיקות לחות כדי לדמות תנאים קיצוניים בעולם האמיתי. | מבטיח שהשבבים יוכלו לתפקד באופן אמין במגוון תנאי סביבה, ומשפר את אורך החיים והיציבות של המוצר. | |
3.בדיקות תאימותודא שהשבב פועל כראוי עם רכיבים או מערכות אחרות, וודא שאין תקלות או פגיעה בביצועים עקב אי תאימות. | מבטיח פעולה חלקה ביישומים בעולם האמיתי על ידי מניעת בעיות תאימות. |
3.3 אריזה ואחסון
לאחר חיתוך פרוסות סיליקון, השבבים הם פלט מכריע של תהליך ייצור המוליכים למחצה, ושלבי האריזה והאחסון שלהם חשובים לא פחות. אמצעי אריזה ואחסון נכונים חיוניים לא רק להבטחת בטיחותם ויציבותם של השבבים במהלך ההובלה והאחסון, אלא גם למתן תמיכה חזקה לשלבי הייצור, הבדיקה והאריזה הבאים.
סיכום שלבי הבדיקה והבדיקה:
שלבי הבדיקה והבדיקה של שבבים לאחר חיתוך פרוסות סיליקון מכסים מגוון היבטים, כולל בדיקה ויזואלית, מדידת גודל, בדיקות ביצועים חשמליות, בדיקות פונקציונליות, בדיקות אמינות ובדיקות תאימות. שלבים אלה קשורים זה בזה ומשלימים זה את זה, ויוצרים מחסום איתן להבטחת איכות ואמינות המוצר. באמצעות הליכי בדיקה ובדיקה קפדניים, ניתן לזהות ולפתור בעיות פוטנציאליות במהירות, תוך הבטחה שהמוצר הסופי יעמוד בדרישות ובציפיות הלקוח.
אַספֶּקט | תוֹכֶן |
אמצעי אריזה | 1.אנטי-סטטיחומרי אריזה צריכים להיות בעלי תכונות אנטי-סטטיות מצוינות כדי למנוע מחשמל סטטי נזק למכשירים או פגיעה בביצועיהם. |
2.עמיד בפני לחותחומרי אריזה צריכים להיות בעלי עמידות טובה בפני לחות כדי למנוע קורוזיה והידרדרות בביצועים החשמליים הנגרמת כתוצאה מלחות. | |
3.עמיד בפני זעזועיםחומרי האריזה צריכים לספק ספיגת זעזועים יעילה כדי להגן על השבבים מפני רעידות ופגיעות במהלך ההובלה. | |
סביבת אחסון | 1.בקרת לחותיש לשלוט בקפדנות בלחות בטווח מתאים כדי למנוע ספיגת לחות וקורוזיה הנגרמות מלחות מוגזמת או בעיות חשמל סטטי הנגרמות מלחות נמוכה. |
2.נִקָיוֹןשמור על סביבת אחסון נקייה כדי למנוע זיהום של שבבים על ידי אבק וזיהומים. | |
3.בקרת טמפרטורהקבע טווח טמפרטורות סביר ושמור על יציבות טמפרטורה כדי למנוע הזדקנות מואצת עקב חום מוגזם או בעיות עיבוי הנגרמות מטמפרטורות נמוכות. | |
בדיקה שוטפת | יש לבדוק ולהעריך באופן קבוע את השבבים המאוחסנים, באמצעות בדיקות חזותיות, מדידות גודל ובדיקות ביצועים חשמליות כדי לזהות ולטפל בבעיות פוטנציאליות בצורה יעילה. בהתבסס על זמן ותנאי האחסון, יש לתכנן את השימוש בשבבים כדי להבטיח שהם ישמשו במצב אופטימלי. |
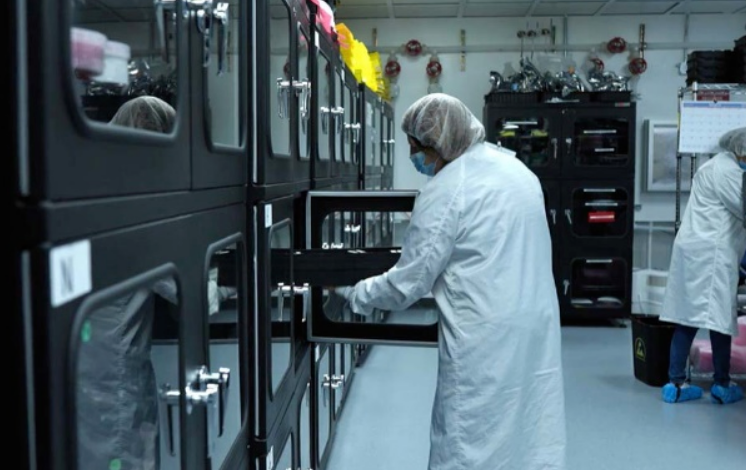
בעיית הסדקים והנזקים הזעירים במהלך תהליך חיתוך פרוסות המזון (wafer) מהווה אתגר משמעותי בייצור מוליכים למחצה. מאמץ החיתוך הוא הגורם העיקרי לתופעה זו, שכן הוא יוצר סדקים זעירים ונזקים על פני השטח של הוופל, מה שמוביל לעלייה בעלויות הייצור ולירידה באיכות המוצר.
על מנת להתמודד עם אתגר זה, חיוני למזער את עומס החיתוך וליישם טכניקות חיתוך, כלים ותנאי חיתוך אופטימליים. תשומת לב מדוקדקת לגורמים כגון חומר הלהב, מהירות חיתוך, לחץ ושיטות קירור יכולה לסייע בהפחתת היווצרות סדקים מיקרוסקופיים ובשיפור התפוקה הכוללת של התהליך. בנוסף, מחקר מתמשך בטכנולוגיות חיתוך מתקדמות יותר, כגון חיתוך בלייזר, בוחן דרכים לצמצם עוד יותר את הבעיות הללו.
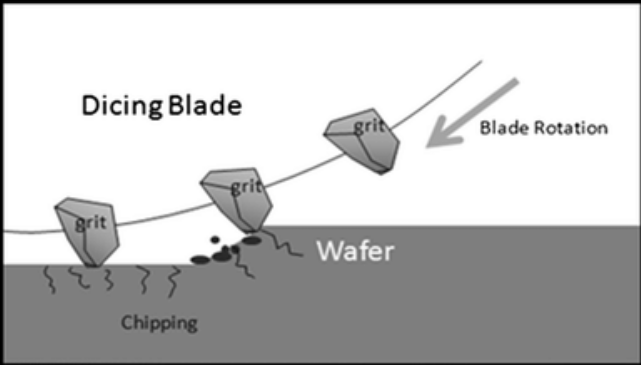
כחומר שביר, פרוסות סיליקון נוטות לשינויים מבניים פנימיים כאשר הן נתונות ללחץ מכני, תרמי או כימי, מה שמוביל להיווצרות סדקים קטנים. למרות שסדקים אלה עשויים שלא להיות מורגשים באופן מיידי, הם יכולים להתרחב ולגרום נזק חמור יותר ככל שתהליך הייצור מתקדם. בעיה זו הופכת לבעייתית במיוחד במהלך שלבי האריזה והבדיקה הבאים, שבהם תנודות טמפרטורה ולחצים מכניים נוספים עלולים לגרום לסדקים קטנים אלה להתפתח לשברים גלויים, מה שעלול להוביל לכשל שבב.
כדי להפחית סיכון זה, חיוני לשלוט בתהליך החיתוך בקפידה על ידי אופטימיזציה של פרמטרים כגון מהירות חיתוך, לחץ וטמפרטורה. שימוש בשיטות חיתוך פחות אגרסיביות, כגון חיתוך בלייזר, יכול להפחית את הלחץ המכני על הוופל ולמזער את היווצרותם של סדקים מיקרוסקופיים. בנוסף, יישום שיטות בדיקה מתקדמות כמו סריקת אינפרא אדום או הדמיית רנטגן במהלך תהליך חיתוך הוופל יכול לסייע בזיהוי סדקים בשלב מוקדם אלה לפני שהם גורמים נזק נוסף.
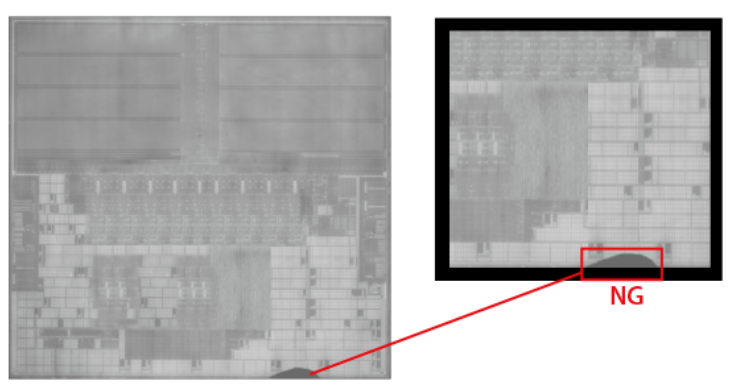
הנזק לפני השטח של הוופל הוא דאגה משמעותית בתהליך החיתוך, מכיוון שהוא יכול להשפיע ישירות על ביצועי השבב ואמינותו. נזק כזה יכול להיגרם כתוצאה משימוש לא נכון בכלי חיתוך, פרמטרי חיתוך שגויים או פגמים בחומר הטבועים בוופל עצמו. ללא קשר לסיבה, נזקים אלה יכולים להוביל לשינויים בהתנגדות החשמלית או בקיבול של המעגל, דבר המשפיע על הביצועים הכוללים.
כדי להתמודד עם בעיות אלו, נבחנות שתי אסטרטגיות מרכזיות:
1. אופטימיזציה של כלי חיתוך ופרמטריםבאמצעות שימוש בלהבים חדים יותר, התאמת מהירות החיתוך ושינוי עומק החיתוך, ניתן למזער את ריכוז המאמץ במהלך תהליך החיתוך, ובכך להפחית את הפוטנציאל לנזק.
2. חקר טכנולוגיות חיתוך חדשותטכניקות מתקדמות כמו חיתוך בלייזר וחיתוך בפלזמה מציעות דיוק משופר תוך הפחתה פוטנציאלית של רמת הנזק שנגרם לפפל. טכנולוגיות אלו נחקרות כדי למצוא דרכים להשיג דיוק חיתוך גבוה תוך מזעור הלחץ התרמי והמכני על הפלפל.
אזור פגיעה תרמית והשפעותיו על הביצועים
בתהליכי חיתוך תרמי כמו חיתוך לייזר ופלזמה, טמפרטורות גבוהות יוצרות באופן בלתי נמנע אזור פגיעה תרמית על פני הוופל. אזור זה, שבו מפל הטמפרטורה משמעותי, יכול לשנות את תכונות החומר, ולהשפיע על הביצועים הסופיים של השבב.
השפעת האזור המושפע תרמית (TAZ):
שינויים במבנה הגבישתחת טמפרטורות גבוהות, אטומים בתוך חומר הוופל עלולים להסתדר מחדש, ולגרום לעיוותים במבנה הגבישי. עיוות זה מחליש את החומר, מפחית את חוזקו המכני ויציבותו, מה שמגביר את הסיכון לכשל שבב במהלך השימוש.
שינויים בתכונות החשמליותטמפרטורות גבוהות יכולות לשנות את ריכוז הנשא ואת ניידותו בחומרי מוליכים למחצה, ולהשפיע על המוליכות החשמלית של השבב ועל יעילות העברת הזרם. שינויים אלה עלולים להוביל לירידה בביצועי השבב, מה שעלול להפוך אותו ללא מתאים למטרה המיועדת לו.
כדי למתן השפעות אלו, שליטה בטמפרטורה במהלך החיתוך, אופטימיזציה של פרמטרי החיתוך ובחינת שיטות כמו סילוני קירור או טיפולים לאחר עיבוד הן אסטרטגיות חיוניות להפחתת היקף ההשפעה התרמית ולשמירה על שלמות החומר.
בסך הכל, גם סדקים מיקרוסקופיים וגם אזורי פגיעה תרמית הם אתגרים מכריעים בטכנולוגיית חיתוך פרוסות ופלים. מחקר מתמשך, לצד התקדמות טכנולוגית ואמצעי בקרת איכות, יהיה צורך לשפר את איכות מוצרי המוליכים למחצה ולחזק את התחרותיות שלהם בשוק.
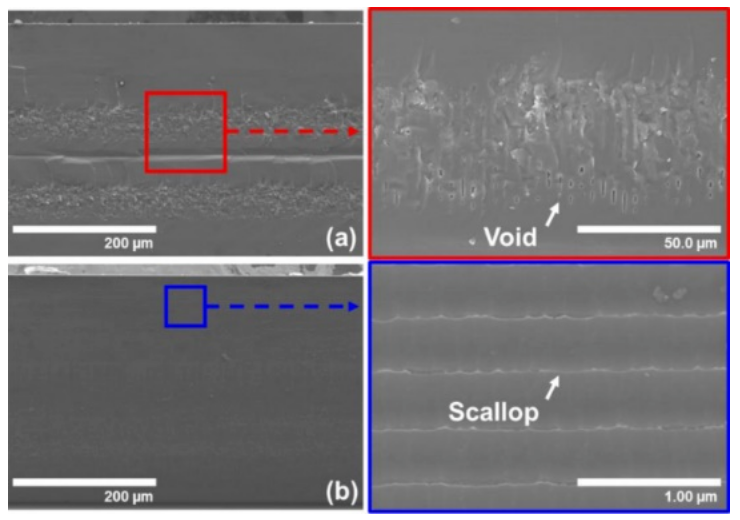
אמצעים לשליטה באזור הפגיעה התרמית:
אופטימיזציה של פרמטרי תהליך החיתוךהפחתת מהירות החיתוך והספק החיתוך יכולה למזער ביעילות את גודל אזור הפגיעה התרמית (TAZ). זה מסייע בשליטה על כמות החום הנוצרת במהלך תהליך החיתוך, דבר המשפיע ישירות על תכונות החומר של הוופל.
טכנולוגיות קירור מתקדמותיישום טכנולוגיות כמו קירור בחנקן נוזלי וקירור מיקרופלואידי יכול להגביל משמעותית את טווח אזור הפגיעה התרמית. שיטות קירור אלו מסייעות לפזר חום בצורה יעילה יותר, ובכך לשמר את תכונות החומר של הוופל ולמזער נזק תרמי.
בחירת חומריםחוקרים חוקרים חומרים חדשים, כגון ננו-צינוריות פחמן וגרפן, בעלי מוליכות תרמית וחוזק מכני מעולים. חומרים אלה יכולים להפחית את אזור הפגיעה התרמית תוך שיפור הביצועים הכוללים של השבבים.
לסיכום, למרות שאזור הפגיעה התרמית הוא תוצאה בלתי נמנעת של טכנולוגיות חיתוך תרמי, ניתן לשלוט בו ביעילות באמצעות טכניקות עיבוד אופטימליות ובחירת חומרים. מחקר עתידי יתמקד ככל הנראה בכוונון עדין ואוטומציה של תהליכי חיתוך תרמי כדי להשיג חיתוך פרוסות פרוסות יעיל ומדויק יותר.

אסטרטגיית איזון:
השגת האיזון האופטימלי בין תפוקת פרוסות ופל (wafer dipping) ליעילות הייצור היא אתגר מתמשך בטכנולוגיית חיתוך פרוסות ופל. יצרנים צריכים לשקול גורמים מרובים, כגון ביקוש בשוק, עלויות ייצור ואיכות מוצר, כדי לפתח אסטרטגיית ייצור ופרמטרי תהליך רציונליים. במקביל, הכנסת ציוד חיתוך מתקדם, שיפור מיומנויות המפעיל ושיפור בקרת איכות חומרי הגלם הם חיוניים לשמירה או אף שיפור התפוקה תוך הגברת יעילות הייצור.
אתגרים והזדמנויות עתידיים:
עם התקדמות טכנולוגיית המוליכים למחצה, חיתוך פרוסות פרוסות (Wraps) ניצב בפני אתגרים והזדמנויות חדשים. ככל שגודל השבבים מצטמצם והאינטגרציה גוברת, הדרישות לדיוק ואיכות החיתוך גדלות באופן משמעותי. במקביל, טכנולוגיות מתפתחות מספקות רעיונות חדשים לפיתוח טכניקות חיתוך פרוסות פרוסות. יצרנים חייבים להישאר קשובים לדינמיקת השוק ולמגמות הטכנולוגיות, תוך התאמה ואופטימיזציה מתמדת של אסטרטגיות ייצור ופרמטרי תהליך כדי לעמוד בשינויים בשוק ובדרישות הטכנולוגיות.
לסיכום, על ידי שילוב שיקולים של ביקוש בשוק, עלויות ייצור ואיכות מוצר, ועל ידי הכנסת ציוד וטכנולוגיה מתקדמים, שיפור מיומנויות המפעיל וחיזוק בקרת חומרי הגלם, יצרנים יכולים להשיג את האיזון הטוב ביותר בין תפוקת פרוסות הוואפל ליעילות הייצור במהלך חיתוך פרוסות הוואפל, מה שמוביל לייצור יעיל ואיכותי של מוצרי מוליכים למחצה.
תחזית עתידית:
עם ההתקדמות הטכנולוגית המהירה, טכנולוגיית המוליכים למחצה מתקדמת בקצב חסר תקדים. כצעד קריטי בייצור מוליכים למחצה, טכנולוגיית חיתוך פרוסות פרוסות (Wraps) עומדת בפני פיתוחים חדשים ומרגשים. במבט קדימה, טכנולוגיית חיתוך פרוסות פרוסות צפויה להשיג שיפורים משמעותיים בדיוק, ביעילות ובעלות, ותוסיף חיוניות חדשה לצמיחה המתמשכת של תעשיית המוליכים למחצה.
הגברת הדיוק:
במרדף אחר דיוק גבוה יותר, טכנולוגיית חיתוך פרוסות סיליקון תמשיך לדחוף את גבולות התהליכים הקיימים. על ידי לימוד מעמיק של המנגנונים הפיזיקליים והכימיים של תהליך החיתוך ושליטה מדויקת בפרמטרי החיתוך, יושגו תוצאות חיתוך עדינות יותר כדי לעמוד בדרישות תכנון מעגלים מורכבות יותר ויותר. בנוסף, חקר חומרים ושיטות חיתוך חדשות ישפר משמעותית את התפוקה והאיכות.
שיפור יעילות:
ציוד חדש לחיתוך פרוסות סיליקון יתמקד בתכנון חכם ואוטומטי. הכנסת מערכות בקרה ואלגוריתמים מתקדמים תאפשר לציוד להתאים באופן אוטומטי את פרמטרי החיתוך כדי להתאים לחומרים ולדרישות עיצוב שונות, ובכך לשפר משמעותית את יעילות הייצור. חידושים כגון טכנולוגיית חיתוך פרוסות סיליקון מרובות ומערכות להחלפת להבים מהירה ימלאו תפקיד מכריע בשיפור היעילות.
הפחתת עלויות:
הפחתת עלויות היא כיוון מפתח בפיתוח טכנולוגיית חיתוך פרוסות סיליקון. ככל שמתפתחים חומרים ושיטות חיתוך חדשות, צפוי כי עלויות הציוד והוצאות התחזוקה יהיו מבוקרות ביעילות. בנוסף, אופטימיזציה של תהליכי ייצור והפחתת שיעורי גרוטאות יפחיתו עוד יותר את הפסולת במהלך הייצור, מה שיוביל לירידה בעלויות הייצור הכוללות.
ייצור חכם ו-IoT:
שילוב טכנולוגיות ייצור חכם ואינטרנט של הדברים (IoT) יביא שינויים מהפכניים בטכנולוגיית חיתוך פרוסות סיליקון. באמצעות קישוריות ושיתוף נתונים בין מכשירים, ניתן לנטר ולמטב כל שלב בתהליך הייצור בזמן אמת. זה לא רק משפר את יעילות הייצור ואת איכות המוצר, אלא גם מספק לחברות תחזיות שוק מדויקות יותר ותמיכה בקבלת החלטות.
בעתיד, טכנולוגיית חיתוך פרוסות סיליקון תביא להתקדמות ניכרת בתחומי הדיוק, היעילות והעלות. התקדמויות אלו יניעו את המשך הפיתוח של תעשיית המוליכים למחצה ויביאו עוד חידושים טכנולוגיים ונוחות לחברה האנושית.
זמן פרסום: 19 בנובמבר 2024